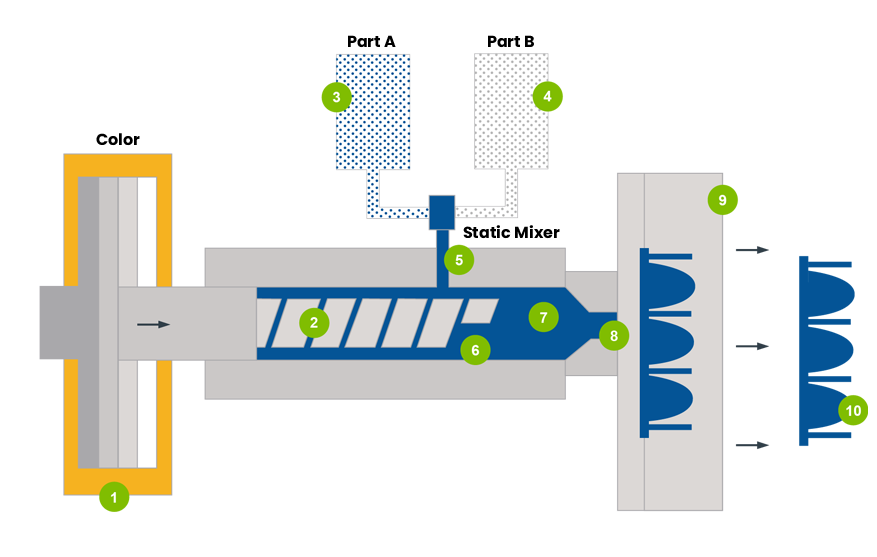
What is LSR Injection Molding?
LSR or Liquid Silicone Rubber molding is an efficient process for manufacturing high-quality silicone parts in medium to high volumes. The process involves using low viscosity silicone elastomer supplied in two-part kits. High precision pumps are used to inject the material into the molding machine's injection unit. Silicone is a bio-inert and biocompatible material widely used in the medical device industry. Its high temperature resistance and excellent physical properties also make it suitable for automotive and industrial applications.
LSR Silicone Keypad, as called as Liquid Silicone Rubber Keypad, Liquid Silicone Keyboard, Liquid Silicone Buttons, which is made of high transparent, high tear strength, good resilience, good water, heat, cold resistant liquid silicone rubber by high precision Liquid Silicone Rubber Injection Molding.LSR Silicone Keypads are widely used in different applications, such as: medical, industrial, instrumentation and communications equipment.
Most Silicone Keypads are molded by compression molding, because compression molding is much cheaper and by using good metal steel, can also have very good quality silicone keypads. While because of liquid silicone rubber's excellent property, more and more customers would like to choose Liquid silicone as a material.
Characteristics of LSR
Silkeypa uses platinum cure silicone compounds to make injection molded parts and sheets. Some key features that make LSR the material of choice for many applications include:
- Wide hardness range of 10 to 80 durometer Shore A
- Wide operating temperature (-58°F to 392°F)
- Good elongation properties
- Excellent electrical insulation
- Excellent UV and ozone resistance
- Excellent for outdoor environmental sealing
- Good for submerged sealing uses (IP67 and NEMA 6)
- Materials include LSR with UL flame ratings UL 94HB and UL 94V-0
- Excellent choice for medical devices
- Certain products meet FDA and USP Class VI requirements
- Good material for low temperature cushioning (cold drop test)
- Many available standard colors and custom colors for molded parts and molded sheets
Silkeypad specializes in liquid silicone rubber injection molding, focusing on this advanced manufacturing process. Our state-of-the-art facilities enable us to deliver a comprehensive range of products and services, spanning from rapid prototyping to the efficient production of high volumes of precision components and parts. Whether you require intricate prototypes or large-scale manufacturing, our expertise in liquid injection molding ensures top-notch quality across the board.
We utilize platinum cure silicone compounds for producing injection molded parts and sheets. Notable attributes that establish LSR as a preferred material for numerous applications comprise:
- Wide hardness range of 10 to 80 durometer Shore A
- Broad operating temperature (−50°C to −200°C)
- Favorable elongation properties
- Exceptional electrical insulation
- Outstanding UV and ozone resistance
- Superb suitability for outdoor environmental sealing
- Effective for submerged sealing applications (IP67 and NEMA 6)
- Material options encompass LSR with UL flame ratings UL 94HB and UL 94V-0
- Ideal selection for medical devices
- Specific products meet FDA and USP Class VI requirements
- Suitable material for low-temperature cushioning (cold drop test)
- Availability of multiple standard colors and custom colors for molded parts and sheet
Electrical Properties of Liquid Silicone Rubber:(values shown are approximations) | ||
Content Resistance | 20 - 200 ohms | |
Contact Rating: | 30 mA at 12 VDC | |
Contact Bounce: | <20 mS, typical | |
Insulation Resistance: | >100 M ohms at 500 |
Silicone Rubber Injection Molding Process
1.Silicone Material Preparation:
The process begins with two separate components, Part A and Part B, pumped through hoses to the static mixer. Part A contains the base material, while Part B contains the catalyst. Additionally, color is pumped to the mixer via another hose. The mixed components are then fed into the injection molding barrel through a shut-off valve, completing the silicone rubber injection molding process.
2. Sealing against Molded Parts:
Once the silicone material is inside the barrel, a shot of the cooled mixed silicone is injected into the mold while the nozzle seals firmly against the liquid silicone rubber.
3. Injection:
The nozzle shut-off valve opens, and a measured shot of cooled liquid silicone is injected into the hot (275F to 390F) clamped silicone rubber mold.
4. Barrel Retraction:
The nozzle shut-off valve opens, and the barrel retracts from the liquid silicone mold as the screw prepares another measured shot of cooled liquid silicone.
5. Repeating the Procedure:
After the cycle is complete, the mold opens, and the molded part and flashing can be removed automatically or by an individual worker. The mold then closes and repeats the procedure.
6. Post-Molding Process:
Following the removal of the molded article from the mold, the post-molding process may involve demisting, post-curing, inspection, and packing.
Introduction to LSR Injection Molding Technology
LSR injection molding is an advanced manufacturing method that transforms liquid silicone rubber material into desired shapes through injection into molds, utilizing pressure and curing processes. Here are the key steps involved in this technology:
Mold Design and Manufacturing: With our experienced design team and state-of-the-art manufacturing equipment, we produce high-precision molds tailored to your specific requirements and design specifications.
LSR Injection: Through precise injection systems, liquid silicone rubber material is injected into the molds, filling the mold cavities and intricate geometries.
Curing and Demolding: Once the material adequately fills the mold, the curing process begins. By controlling curing time and temperature, the liquid silicone rubber gradually solidifies into the desired shape. The mold is then opened, and the molded parts are demolded.
Benefits of Silicone Injection Molding
- High-Volume Production: Advanced LSR materials enable cost-effective, high-volume production of intricate liquid silicone injection molding parts.
- Minimal Contamination Risk: Liquid injection molding (LIM) employs automated machines, reducing human interaction with materials. Unlike labor-intensive compression molding, LIM offers lower contamination risk. Fully automated liquid injection molders further minimize contamination, with ISO-certified clean rooms ensuring hygienic production.
- Swift Cycle Time: LSR component cycle time hinges on factors like mold temperature, material arrival at the mold, component geometry, vulcanization traits, and curing material chemistry. Preheating the injection barrel and cold runner to 40-80 degrees Celsius accelerates curing for two-part, platinum-cured LSRs.
- Flash and Waste Elimination: Molds with minimal runners and flashless operation virtually eradicate material scrap.
LSR Silicone Keypad's Advantages Compared to Solid Silicone Keypad
Liquid Silicone Rubber (LSR) keypads offer a broader Shore Hardness range, spanning from 5 to 90A. In comparison, compression-molded silicone keypads typically start at a minimum hardness of 30A, with recommendations falling in the 50-60A range. The extended Shore hardness options make LSR a compelling choice.
Liquid silicone rubber keypads boast higher precision, featuring minimal parting lines and reduced silicone rubber flashing. Additionally, they maintain stable button designs and exhibit precise size tolerances, with a remarkable tolerance of +/-0.02mm.
One of the significant advantages of LSR keypads is their extended key life. LSR demonstrates superior properties to solid silicone, including higher tear strength, excellent resilience, water resistance, and resilience to both heat and cold. Furthermore, LSR is characterized by high transparency.
Efficiency is a key factor favoring LSR keypads in production. The elimination of manual material placement and shorter shot cycle times contribute to higher production efficiency. This not only streamlines the manufacturing process but also enhances overall productivity.
In summary, LSR keypads stand out due to their wider Shore Hardness range, precision in design, longer key life, superior material properties, and increased production efficiency, making them a compelling choice for applications requiring silicone keypads.
Why Choose Silkeypad for LSR Injection Molding Service?
Material Versatility: Opting for the right material to enable flexibility and customization is crucial in product creation. LSR empowers customers with this capability.
Extreme Temperature Resilience: LSR maintains its properties across a wide temperature range, from –76°F to +365°F, making it well-suited for parts enduring diverse temperature conditions.
Wide Range of Applications: With a broad durometer spectrum and additive compatibility, LSR is adaptable for various applications, enhancing its properties as needed.
Resilience to Environmental Factors: LSR boasts high resistance to chemicals, water, oxidation, and compression set, ensuring extended service life and minimizing maintenance requirements.
Medical Suitability: LSR's bio-compatibility, non-toxicity, and resistance to bacterial growth make it particularly fitting for medical equipment.
Electrical and Chemical Resistance: LSR's robust resistance to high electrical current and chemicals makes it an excellent choice for high-voltage environments.
Industry-Specific Applications: Beyond medical equipment, LSR benefits numerous industry-specific parts, showcasing its wide-ranging applicability.
Expert Design Support: Silkeypad's team enables innovative and precise design of LSR molded parts and provides comprehensive customer support throughout the process.
Related Custom Solutions from Silkeypad
Production Capabilities
Single-Shot Molding: In this molding process, only one LSR material is used for injection molding parts.
Multi-Shot Molding: LSR is combined with two or more polymers or a polymer and substrate in this process for more complex components.
Overmolding: In overmolding, the liquid silicone rubber is molded around a substrate or finished component.
Micromolding: This injection molding process produces tiny, complex parts, typically with a shot weight of less than 1 gram.
Hygienic Molding: LSR parts are produced in a clean, hygienic environment that is highly controlled to various levels, such as white rooms or more stringent ISO cleanrooms with various classifications.
Liquid Silicone Rubber Part Production
Liquid injection molding (LIM) is a versatile process for molding silicone rubber into a wide range of parts and products. Unlike traditional reaction injection molding (RIM) that utilizes pressurized impingement mixing, LIM employs mechanical mixing. This method combines a two-component platinum-cured LSR material compound, which then flows into a mold.
A key distinction between LSR LIM (liquid injection molding) and thermoplastic injection molding lies in material delivery. The LSR injection tool resides in an LSR-specific injection molding press. This specialized setup ensures precise shot size control, enabling consistent production of liquid silicone rubber components.
LSR Quality Standards
Your silicone rubber molding manufacturer must meet rigorous specifications and maintain a strong commitment to quality throughout product design, tooling, prototyping, and parts production. Essential quality standards for liquid silicone rubber injection molding encompass:
- Advanced Quality Planning
- Custom Validations and Qualifications
- Control Plans
- Customized Procedures
- Wide-ranging Metrology Capabilities
Early quality planning, visual inspections, and material and part testing ensure quality. ISO certifications like ISO 9001, ISO 13485 for the medical industry, and IATF 16949 for the automotive sector provide further assurance that your LSR parts manufacturer adheres to robust quality systems, guaranteeing consistent high-quality parts.
Applications of LSR Injection Molding
Liquid silicone rubber injection molding finds application in numerous industries, including medical, healthcare, automotive, infant care, consumer food and beverage, appliance and electronic products, and industrial sectors.
Life Science
LSR finds extensive use in medical applications due to its inert qualities, biocompatibility, and stability in rigorous environments. Numerous life sciences products feature components with intricate details, tight tolerances, small part geometries, and enhanced cleanliness. Respirator masks, valves, diaphragms, surgical instruments, and drug delivery devices are among the critical applications where LSR is favored.
Automotive
In the automotive industry, LSR's exceptional performance in extreme temperatures and UV light makes it ideal for various components, including wire harness seals, connectors, bellows, gaskets, vibration dampeners, housings, and sensors.
Consumer Products
LSR is chosen for consumer products due to its versatile properties. It creates watertight barriers, bacteria-resistant showerheads, and faucets, vibration-resistant sealed housings for hygiene products, soft surfaces for headphone and hearing aid tips, and safe baby bottle tips. LSR's performance in various environments and temperature ranges also makes it suitable for valves, gaskets, and diaphragms in appliances.
Industrial Application
Industrial products require durability in challenging environments, making LSR ideal for valves, gaskets, and sealed housing in safety devices like smoke detectors. For sensitive applications like furnaces and gas water heaters, LSR's stability is crucial. It withstands chemicals and high heat while maintaining form, ensuring reliable performance in manufacturing equipment, safety devices, and other reliability-demanding projects.